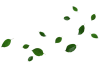
Our quest for beauty inspires us in the design and development of our high-end lighting systems. Our creations are high-tech, aesthetically pleasing and highly sustainable, and aim to enhance the status of architectural spaces.
We combine a sartorial approach based on meticulous attention to detail with industrial production using advanced machinery and a virtuous circular approach.
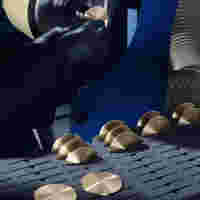
A path of growth and specialisation
In 2001, we had the courage to invest in LED technology. Our vision has enabled us to anticipate trends and establish ourselves as a highly specialised and leading brand in the field of precision industrial design. With over 30 Italian and European patents filed over the years, we have become a benchmark in the high-end architectural lighting sector.
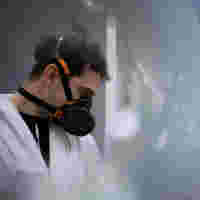
Made in Florence
All our products are designed and manufactured entirely in our factories in Florence. Each stage of the production process is monitored with the utmost care and attention to detail. We use automated 4.0 and 5.0 systems, which are essential for fully integrated management of the entire supply chain. Our philosophy also allows us to support local suppliers and reduce environmental impact by minimising the transport of materials and goods.
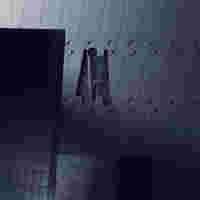
Aesthetics, technology, functionality.
To us, design is not just about aesthetics; it is the perfect synthesis of beauty and functionality. To this end, we collaborate with talented designers to create integrated solutions and high-quality products that have won numerous awards in Italy and abroad, which is testament to the strength of this vision.